Buying blenders wholesale is a great opportunity for businesses, entrepreneurs, and even organizations, whether for resale, marketing, or supplying retail chains. This article offers a detailed analysis of the wholesale market for blenders, detailing the principal considerations, advantages of buying in bulk, and advice on prudent purchasing. Readers will learn how to assess quality, develop pricing plans, select trustworthy suppliers, and handle logistical problems like shipping and storage. By the end of the article, one will have sufficient information and knowledge to make wholesale purchases of blenders with the utmost confidence.
What Should You Know About Blender Wholesale?
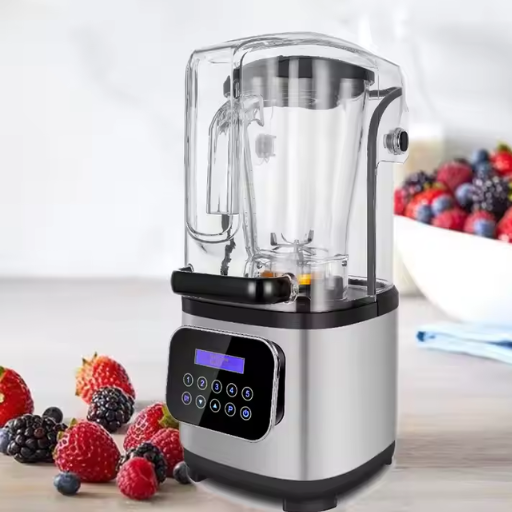
In a blender wholesale transaction, a multitude of critical facets that stem from the purchasing decision must be taken into account. Start by understanding the quality and specifications of the blenders by looking at the features which include motor power, blade strength, durability, and warranty. Following this, comprehend the pricing tiers that are commonly used in a wholesale transaction; these include discount policies, MOQs, and seasonal discounts. It is also important to identify credible suppliers first; emphasize vendors that have proven track records, good ratings, and effective communicators. Moreover, procurement does require planning such as shipping costs, lead times, and space for storage which ensures the elimination of inefficiencies in the procurement process. Following this, analyzing these factors would help to obtain superior products at competitive prices without risking too much.
Understanding the Price Dynamics in Wholesale Blenders
To analyze price changes of wholesale blenders, one has to consider a few elements. Importance in wholesale pricing is given to production expenses, raw material quality, and market demand. An example of a pricing factor would be the Minimum Order Quantity (MOQ), which places a cap on the most acceptable amount of units a vendor has to buy to qualify for bulk pricing. Suppliers usually have a system of discounts at different levels, where purchasing a higher number directly results in a low cost for each unit. Furthermore, there are also seasonal price changes as well, for example, during certain months of the year like holidays, there is an increase in demand which may increase price levels for a short period.
Shipping charges are another factor that should be kept in mind because they impact total expenses. Freight charges, customs duty, air freight, and sea freight are dependent on order size and time of delivery. These charges impact the total costs of making a purchase decision. Vendors also estimate lead times, which come at a premium these days, resulting in higher expenses. Established suppliers are known to offer provision pricing, thorough cost analysis, and accommodating terms. This is done to give the buyer control over expenses. Effective management of the budget enables the buyer’s objectives vet achieved. It is possible to achieve prices that beat competitors without any trade-offs on quality or dependability in the wholesale blender industry by combining order planning, negotiations, and evaluation of the supplier’s credibility.
Key Considerations in Choosing the Right Distributor
Selecting the right distributor requires a look into multiple key factors to ensure that their operations are compatible with the business requirements. To begin with, check how the distributor is perceived in the market and their past performance. Trustworthy distributors always comply with set timely deliveries, and product standards, as well as adequate after-sale services. It is also crucial to check customer reviews and ratings since they can indicate how the distributor performed in the past.
Secondly, look into the distributor’s capabilities of managing their inventories. Make sure that adequate stock is available to cater for demand tolerances, especially during the peak seasons. Distributors with efficient systems for tracking and supply can provide timely updates on orders, which removes a great deal of uncertainty and delays.
How much to charge and how to get paid matter a great deal too. A comprehensive list of the terms of service should be presented including obscure costs like shipping, handling, and storing products. Volume suppliers or distributors with a flexible payment form can significantly cut costs, thus increasing budget efficiency.
Finally, the utilization of communication and an understanding of the technological components are crucial. Make sure the distributor has a support team that can respond to inquiries and effectively solve issues as they arise. For industrial products like blenders, the capacity of distributors to differentiate deeper into the specifics of the products brings additional value by helping to select optimal solutions for particular uses. By checking these factors from several trustworthy providers, companies can pinpoint distributors that guarantee savings without sacrificing dependability.
Evaluating Product Description and Specifications
Assessment of the description of products as well as product specifications entails a unique level of attention to detail as it pertains to their fit in the operational needs and performance demands. Effective product descriptions should outline central features including scope, weight, constituting materials, power requirements, and certification of the product industry. These details furnish the user with the necessary knowledge regarding the product’s capabilities along with the limitations.
When checking specifications, always cross-reference to your operational requirements. For example, industrial equipment must pass workload capacity, safety norms, and energy efficiency standards. Manufacturer’s pages, professional review websites, and industry-specific online shops serve as the best sources of authoritative and reputable concise information. In this case, synthesizing information from top sources helps in spotting consistent information, discrepancies, and valuable data such as user comments and performance metrics. These sources guarantee precise informed decision-making without ambiguity.
How to Buy Wholesale Blenders Effectively?
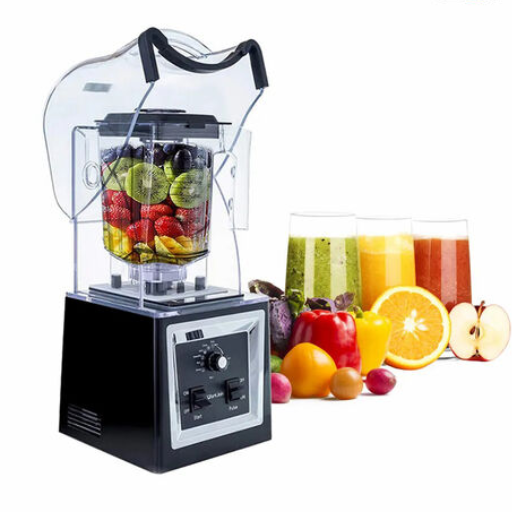
Evaluation of Selected Factors Helps in Business Wholesale Blenders Purchase. First pointers to check consider are the power rating, blade type, pitcher size, and the motor’s ruggedness. These factors affect performance and durability, especially when intensive use is required.
While checking for bulk suppliers, confirm that the blenders meet warrants of safety standards such as UL, CE, or Energy Star to guarantee quality and energy efficiency compliance. Consider warranty terms, bulk pricing, and customer support policies from different suppliers. In addition, check their maintenance and long-term reliability through customer reviews.
Settle with the more reputable suppliers, make sure you check on the payment terms as well as on the deadlines for the delivery to meet operational deadlines. Taking such approaches guarantees low costs without affecting internal efficiency and quality.
Key Factors to Consider: Blade Quality and Motor Efficiency
Regarding blade quality, the most important aspect is the construction of the blade. Therefore, select a blade made from stainless steel since it is the most durable and offers rust-free cutting with accuracy. A well-designed blade should be sufficiently sharp and allow for the effortless handling of tougher ingredients, thus enabling smoother blends without overworking the motor. You should also decide whether the blades are detachable to make cleaning and maintenance easier.
To focus on motor efficiency, check the wattage or horsepower rating of the motor. For blended jobs, 600 to 1,500 watts is optimal, considering heavy-duty tasks such as ice crushing or blending of fibers require higher power. Also, strive for thermal protective motors to avoid overheating after extended use. Quieter motors tend to be of superior quality and perform consistently over time. By ensuring that both blade quality and motor efficiency are given equal attention, blenders can be obtained which promote lower maintenance and greater function efficiency during commercial operations.
Ensuring Reliable Shipping and Delivery Options
Cost-effective options for shipping services and delivery schedules are very crucial to customer satisfaction and operational cost-effectiveness. To determine logistics reliability the prime consideration must be given to those who have delivered timely consignments, regularly, coupled with sound structural support. Assess their operational metrics such as service availability and punctuality records and make sure those are up to your expectations. On top of that, these issues should be taken into consideration: Choose vendors who have real-time tracking systems so that proactive mitigation and management can take place. Additionally, these service providers should be able to offer flexible shipping options, such as overnight shipping, shipping to multiple locations, etc. Lastly, in the case of cross-border shipping, ensure the provider’s competence in stores and regulatory compliance to avoid hampers. Working with a contractor, who offers speedy delivery and ensures accuracy in consignment details will foster better customer confidence and aid in building a more reliable supply chain.
Tips for Choosing the Best Brand and Model
- Define Your Requirements: Start by identifying the specific needs and applications for the product. Determine essential features such as performance, durability, size, or specific technical functionalities that align with your purpose. For example, if you are focusing on electronics, consider factors like processing speed, memory capacity, and compatibility.
- Research Brand Reputation: Opt for brands known for their consistency in quality and customer support. Look for independent reviews, expert ratings, and customer feedback to evaluate the reputation of the brand. Popular, well-established brands often offer better warranties and after-sales services, which are critical for long-term reliability.
- Evaluate Technical Specifications: Compare models based on their specifications and features. Analyze core details like build material, efficiency, energy consumption, and compatibility with your existing systems or tools. Choose models that not only meet industry standards but also offer innovative upgrades that may enhance productivity or long-term usability.
- Cost and Value Analysis: It is essential to assess the price against the features provided. Avoid choosing based solely on cost—prioritize value instead. A higher upfront investment in a superior model often results in reduced maintenance costs and an extended life span.
- Consider Customer Feedback and Experts’ Opinions: Analyze both user experiences and professional reviews. Forums, comparison tools, and product testing websites can offer detailed insights into real-world performance issues or advantages that may not be apparent from surface-level descriptions.
- Check Warranty and Support Options: Ensure that the brand provides robust warranty terms and easily accessible customer support. A strong post-purchase experience fosters trust and ensures consistent operations, especially for high-use or critical equipment.
By combining these steps with methodical research, you can confidently decide on the best product brand and model that aligns with your operational or personal requirements.
Why Choose Commercial Blender for Your Business?
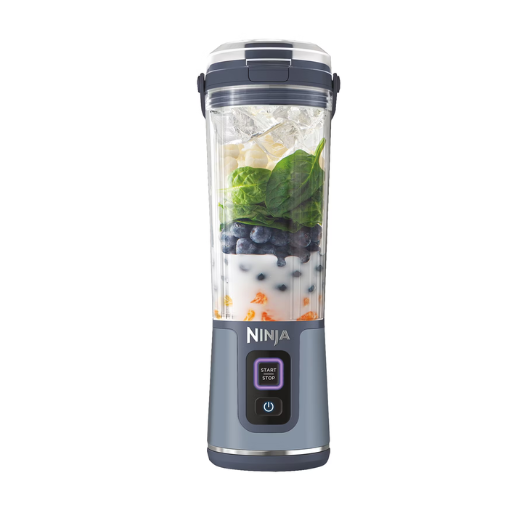
Rests, cafes, and juicers benefit from high-performance commercial blenders that are custom-designed to meet rigid operational requirements. Commercial blenders are a must-have for any perishable food-related enterprise. They’re designed to operate at higher volumes of workloads and enable endurance during prolonged use. Commercial blenders are built using rigid materials that withstand rough use and contain powerful motors allowing for continuous blending of smoothies, sauces, soups, and other items. Furthermore, variable speed control alongside specialized attachments provides commercial blenders with the ability to serve unmatched versatility. The invaluable feature of developing solutions with less time invested, developing superior grade products, and enhanced customer satisfaction all accompany investing in a commercial grade blender for a business.
Advantages of Using Commercial Blender for Bulk Processing
- High Efficiency and Time Savings
Commercial blenders are built to process large quantities of ingredients in minimal time, significantly reducing preparation time for high-demand environments. Their robust motors and advanced blade technologies allow for quick and efficient blending, making them ideal for bulk processing of smoothies, soups, sauces, and more.
- Consistent and High-Quality Results
Equipped with precision-engineered components, commercial blenders ensure uniform blending, even for tough ingredients like ice, nuts, or fibrous vegetables. This consistency ensures that every batch meets the same quality standards, critical for maintaining customer satisfaction and brand reputation.
- Durability and Longevity
Constructed with high-grade materials such as stainless steel and industrial-grade plastics, commercial blenders are designed to withstand continuous, intensive use. This durability minimizes downtime and ensures a long operational lifespan, delivering a high return on investment for businesses.
- Versatility for Diverse Applications
With variable speed settings, pre-programmed functions, and specialized attachments, commercial blenders offer unparalleled versatility. They can handle tasks such as pureeing, emulsifying, grinding, and even chopping, making them a multifaceted tool in any commercial kitchen.
- Cost-Effectiveness in Bulk Operations
By reducing processing times, minimizing waste, and delivering consistent quality, commercial blenders contribute to overall operational efficiency. Their ability to handle bulk tasks reduces labor-intensive processes and optimizes workflow, providing a measurable impact on cost savings.
The Importance of Durable and Stainless Steel Construction
The stainless steel construction used in the commercial-grade kitchen equipment guarantees longevity and reliability in functionality. Stainless steel does not corrode, easily wear out, or react with extremely high temperatures making it ideal for harsh environments. Its non-reactive properties assist in maintaining food quality and also matching the stringent hygiene requirements. Since stainless steel does not require much upkeep, the equipment has an increased life span and replacement frequency decreases. Additionally, its robust structural integrity means the equipment can withstand the strain from rigorous usage while still performing efficiently supporting optimal operational productivity.
How Commercial Blenders Enhance Kitchen Efficiency
These days, commercial blenders hold the utmost importance in the business world. Their high motor speeds alone accomplish tasks unmatched by standard blenders. Additionally, commercial-grade options are more versatile. Rather than being used for blending or pureeing, they can also be employed for grinding, making them easy to use on a large scale. This multifunctional technology minimizes preparation time, giving greater freedom to chefs during peak hours. As the blender is equipped with precision controls, the required blending consistency or texture is obtained which is imperative for food hydration. In addition, the efficient and extensive use of these blenders in separate facilities is guaranteed due to durable components like stainless-steel blades or reinforced containers. Ultimately, incorporating a commercial-grade blender into the work center optimizes task flows, increases performance, and minimizes time waste.
Are Portable Blenders a Viable Option?
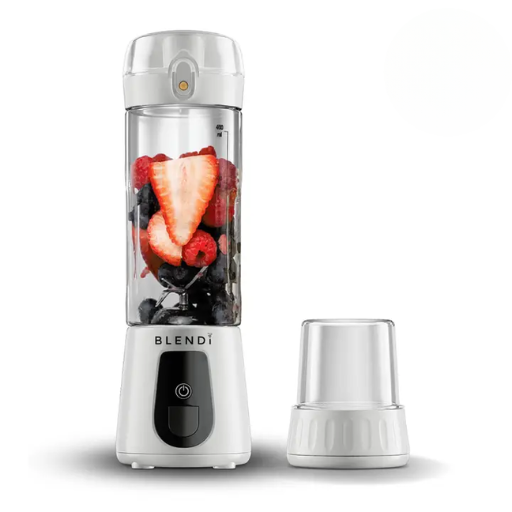
Portable blenders are useful in very specialized scenarios. These devices are optimized for single servings and are intended for easy transport. Because these devices are compact, they are ideally structured for mobility. These blenders are often powered by rechargeable batteries. Thus, these devices are great for people who have limited access to power. Still, their motor power and overall capacity are lower compared to commercial-grade devices which renders them incapable of completing heavy-duty tasks or handling large volumes. They do serve a purpose, however, and portable blenders are quite proficient in light blending tasks like smoothies and protein shakes. Unfortunately, these devices fall short in scenarios where high volumes of blending are required.
Assessing the Convenient Nature of Portable Blenders
Blenders that can be carried around are most efficient and convenient because they are lightweight, compact in size, and do not require any cords. They offer effortless preparation of single-serving drinks, making them perfect for people with active lifestyles and even those who travel often. Many models are outfitted with USB rechargeable batteries which further increases usability in various settings such as offices, outdoor trips, or gyms. Moreover, their ease of use and cleaning makes them perfect for informal, everyday scenarios. On the other hand, their usefulness comes with trade-offs; the majority of portable blenders possess a weaker motor and smaller containers, making it difficult to use harder components like ice or large portions. They will certainly not replace traditional automobile blenders or professional kitchen blenders, but they do represent a practical solution for frequent light-duty blending tasks.
Comparing Size and Color Options for Portable Use
Portable blenders come in varying sizes, typically ranging from 10 to 20 ounces in capacity, catering to the needs of users seeking single-serving solutions or slightly larger portions. Compact models prioritize portability, fitting easily into backpacks or gym bags, while slightly larger options provide more versatility without compromising mobility. Regarding color options, manufacturers offer a broad spectrum to suit diverse preferences, from neutral tones like black, white, or gray to vibrant colors such as blue, pink, or green. This variety enables users to select a blender that matches their personal style or kitchen aesthetic. It is important to choose a size and color that aligns with the primary usage environment and personal needs for optimal satisfaction.
The Role of Electric Portable Blenders in Home Appliance Markets
The electric portable blender industry has emerged as a growing category within home appliances, being fueled by the global trend of health and mobility where greater importance is placed on consumer convenience. Their compactness enables users to remain within the confines of a health-conscious lifestyle by swiftly preparing smoothies, protein shakes, and other beverages to meet the increasing demand for on-the-go nutrition. Moreover, with market growth advanced battery technology is further propelling the industry by providing greater power and endurance while keeping portability. In addition, manufacturers are now adding features such as USB-rechargeable batteries, durable stainless steel blades, and safety interlocks that cater to modern consumer needs, further ensuring product usability. This makes the blender suitable for a variety of settings, whether at home, in the office, or when engaging in outdoor activities. The small eco-friendly materials used as well as the energy-efficient design allow the blenders to be sustainable, making them highly impactful in the evolving small home appliance space.
How to Ensure High-Quality Wholesale Blenders in 2024?
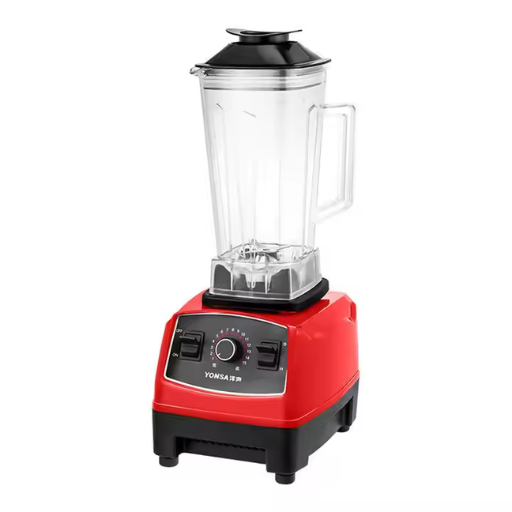
- Material Selection: Ensure that the blenders are made from durable, food-grade materials such as BPA-free plastics and stainless steel. High-quality components are essential for longevity and user safety.
- Performance Standards: Prioritize blenders with advanced motor technology and efficient blade designs that can handle a variety of tasks, from crushing ice to blending tough ingredients smoothly and consistently.
- Energy Efficiency: Look for models designed with energy-saving features and minimal environmental impact, aligning with growing consumer demand for sustainable appliances.
- Technology Integration: Choose products featuring modern advancements such as USB-rechargeable batteries, intelligent speed control, and noise reduction systems to cater to diverse user requirements.
- Compliance and Certification: Verify that the blenders meet international quality standards and certifications, such as ISO or CE markings, to establish credibility and trust in the marketplace.
- Supplier Reputation: Work with reputable suppliers known for rigorous quality control processes and timely, reliable delivery to ensure product consistency and availability.
By focusing on these aspects, you can confidently source high-quality wholesale blenders that meet modern consumer expectations and stand out in the competitive market.
Verifying Seller Credentials and Buyer Feedback
Begin by validating the seller’s profile to make sure that your transaction is successful. A business license, a contact number, and even their years of experience in the field matter greatly. In addition to that, search for previous customers’ reviews on independent sites to verify if they can be relied on and whether or not the product they sell is valuable. Trustworthy sellers generally issue certifications or documents proving they have met all the requirements of the industry to endorse them.
In the same manner, analyze buyer comments for consistent mentions of product effectiveness, punctuality of delivery, and efficiency of customer feedback. Trustpilot, Google Reviews, and other business directories provide valuable feedback of this sort. Focus particularly on the methods the seller employs to address complaints, as that reveals a lot about his customer service levels. This information, when combined, helps in making a better business decision and avoiding the risks that come with wholesale buying or selling.
Exploring Custom Package Options
Tailor-made solutions are available for a range of industries, from software development to logistics and consumer goods. When evaluating custom software packages, factors like their functions, how scalable they are, and their integrations with current systems need to be taken into consideration. The main goal for tailor made packages is to enhance usability, improve efficiency and cater to niche requirements that standard solutions cannot address.
Custom software packages permit businesses to implement specific solutions that address industry challenges. Popular tools and platforms already allow flexibility for developers to change the algorithm, interface, or other APIs and still perform well. As well as in software, in logistics realms a custom-packaging solution focuses on materials, structure, cost, and environmental impact to enhance the security of transported goods. Usually, however, the selection of the right provider hinges on service, their ability to innovate, and compliance with the law.
In order to take maximum advantage and get the most desirable outcomes from custom packages, a business needs to utilize reliable sources to compare their goals with custom packages on offer. When evaluating prospective suppliers, make sure you know what is at stake, so you know what guidance to provide and what transparency, costs, and customization options need to set out in case studies.
Analyzing Stock Availability and Future Viewing Trends
Stock availability and future viewing trends require a comprehensive analysis of market data, consumer behavior, and emerging technological advancements. Based on information consolidated from leading websites, effective stock availability monitoring depends on real-time inventory management systems, predictive analytics, and supply chain transparency. These ensure that demand fluctuations are managed efficiently, minimizing stockouts and overstock scenarios.
Regarding future viewing trends, streaming platforms dominate forecasts as consumers increasingly favor on-demand, personalized content. Advancements in artificial intelligence and machine learning are further shaping viewing experiences, allowing tailored suggestions and dynamic content delivery. Additionally, technologies like virtual and augmented reality are expected to create immersive environments, enhancing user interaction and engagement. These insights underline the evolving nature of viewer preferences and the necessity for data-driven strategies to anticipate and adapt to future trends.
References
Frequently Asked Questions (FAQ)
Q: What should I consider when selecting a wholesale blender?
A: Consider factors such as the type of beverages you plan to make, the blender’s power and capacity, and whether it can handle the demands of daily use. Look for models that can effortlessly blend smoothies, fresh juice, or even soups and sauces. Ensure the blender fits your countertop and kitchen appliance needs.
Q: How can I find high-quality blenders for bulk purchases?
A: Look for reputable b2b suppliers or factories that specialize in kitchen appliances. Ensure they offer a selection of wholesale blenders with high quality and durability. Visit us or check online platforms for reviews and detailed product info.
Q: What is the typical minimum order quantity for wholesale blenders?
A: The minimum order quantity can vary, but it often starts at around 1000 units. This can depend on the supplier’s policies, so it’s best to contact them directly to arrange an order that suits your needs.
Q: Can I customize blenders with my company’s logo?
A: Yes, many suppliers offer customization options, including adding your company’s logo to the blenders. This is an excellent way to promote your brand and can be arranged directly with the supplier.
Q: Are there automatic blenders available for wholesale?
A: Yes, there are automatic models available that can save time and effort in preparing smoothies, milkshakes, and other beverages. These are ideal for high-demand settings like cafes or restaurants.
Q: What are the benefits of buying blenders in bulk?
A: Buying in bulk can offer competitive pricing and ensure a consistent supply of high-quality products. It is also efficient for businesses that need to stock a variety of blenders for different settings or client needs.
Q: How can I ensure the blenders are suitable for making fresh juice and smoothies?
A: Check the specifications for features like powerful motors, durable blades, and the ability to handle frozen fruits or ice. These features are crucial for making fresh juice and smoothies efficiently.
Q: What support can I expect from suppliers when buying wholesale blenders?
A: Suppliers typically offer customer support to help with product selection, freight arrangements, and after-sales service. Don’t hesitate to ask for recipe ideas or blender usage tips to maximize your purchase.
Q: Can I get info on additional kitchen appliances when purchasing blenders?
A: Many suppliers offer a broad selection of kitchen appliances alongside blenders. You can request more info on items like juicers, mixers, or electronic gadgets to complement your purchase.
Q: How do I calculate the total cost of a bulk blender purchase?
A: The total cost will include the price per item, any customization fees, freight charges, and applicable taxes. Suppliers can provide a detailed quote to help you calculate the overall expense accurately.